At 6pm on March 16, 2022, after six hours of intense work, the lifting system consisting of 16 large hydraulic lifters steadily lifted the welded ball space frame structure with weight more than 1,400 tons by 11.2 meters and then reached the designated position, successfully completing the overall lifting operation, marking that Jingdezhen International Ceramic Culture Expo and Tourism Exchange Center, the largest and internationally influential ceramic exhibition and exchange welded ball space frame structure center built by China Railway No.4 Bureau, has entered the final construction sprint stage in an all-round way. The construction project of Jingdezhen International Ceramic Culture Expo Tourism Exchange Center is located in the north of Yingbin Avenue, south of Hongyuan Road and east of Sishan Road, Jingdezhen City, Jiangxi Province, with a land area of 75,954.2 ㎡ and a total construction area of about 90,000㎡ with welded ball space frame structure .
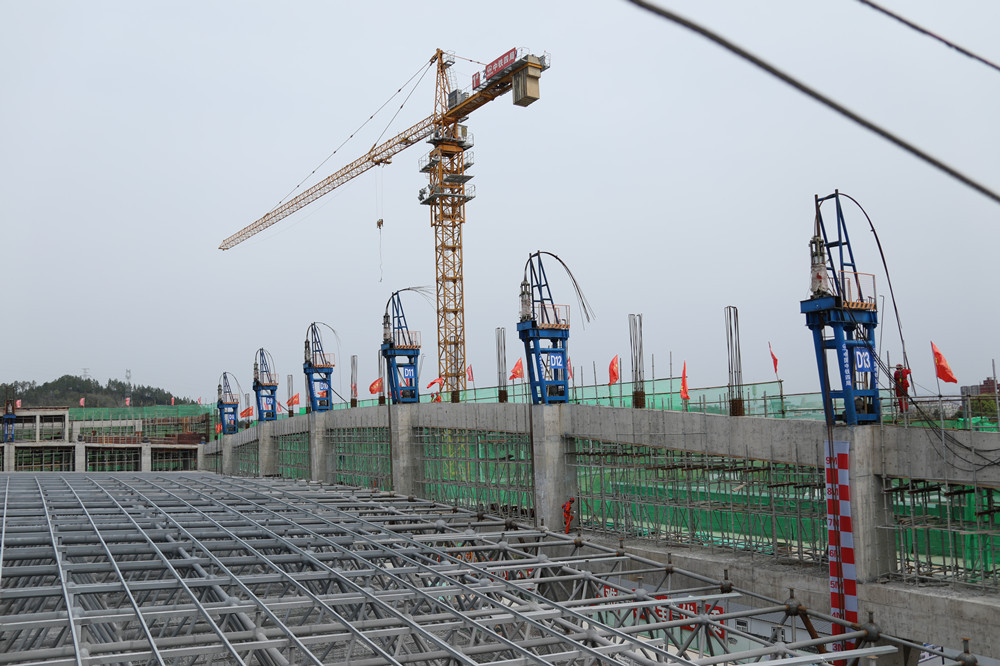
It is the largest welded ball space frame structure ceramic Expo Exchange Center project in China. The construction content of the project includes 35,000m2 ceramic Expo Center, 15,000m2 conference center, 10,000m2 supporting rooms, 30,000m2 underground parking lot, roads, squares, greening and other supporting infrastructure projects.
Optimization of equipment intelligent monitoring, solving the technical problems of overall lifting of large structures . The welded ball space frame structure construction project of Jingdezhen International Ceramic Culture Expo Tourism Exchange Center is 290m long, 141m wide and 24m high, with one floor above ground and two local floors. It is divided into four functional areas: the east hall, the west hall, the horizontal hall and the preface hall. The roof structure of the east hall and the west hall is extremely symmetrical, and the east hall, the west hall and the horizontal hall all adopt the special-shaped welded ball grid structure. The projected size of the grid in the welded ball space frame structure East Exhibition Hall, which has completed the overall upgrading of the grid structure, is 74.4m*125.4m, with a total weight of about 1,400 tons. There are 16 designed lifting points, which are respectively arranged on the surrounding supporting columns, and the overall lifting height reaches 11.2m The maximum height difference of each point in the upgrading process should be strictly controlled within 10mm, so the difficulty of its operation can be imagined. How to safely and accurately lift such a "monster" to the designated position has become a difficult problem for the project builders. After investigation and simulation, it is found that the traditional lifting equipment with a single stroke of 250mm is not enough to complete this important task, which undoubtedly increases the difficulty of lifting the grid. In order to control the lifting deviation, the technical team of the project decided to choose a piercing jack with a single stroke of 500mm for lifting after repeated research. "Compared with the traditional lifting equipment with a single stroke of 250mm, this effectively reduces the number of steel strand clamping pieces, reduces the deviation caused by different tightness of clamping pieces among lifters, and ensures that the lifting process is efficient, stable, synchronous and reliable, which can ensure the safety and quality of the structure." Chen Guoquan, chief engineer of the project, introduced. After the problem of lifting equipment was solved, the project department chose the intelligent synchronous monitoring system based on the Internet of Things to replace the traditional total station manual measurement for automatic synchronous monitoring, because the overall coordination of 16 lifting points in the lifting process was extremely high. In this way, the monitoring data will be analyzed through the platform, and the height difference between the monitoring points and the adjacent points will be displayed on the BIM model in real time. "Compared with the traditional total station measurement and manual analysis, the whole process automatic monitoring technology greatly improves the measurement efficiency, shortens the feedback time, and realizes real-time feedback and early warning without considering the network delay." Chen Guoquan added.
Post time: May-26-2022